
液位产品导航
磁翻板液位计
磁敏电子双色液位计 专用远传变送器 专用报警开关 电加热磁翻板液位计 真空夹套型磁翻板液位计 蒸汽夹套磁翻板液位计 钛合金磁翻板液位计 带远传磁翻板液位计 顶装磁翻板液位计 pp材质防腐磁翻板液位计
玻璃管液位计
螺纹玻璃管液位计 玻璃管液位计 不锈钢管式带扣304玻璃 小型管式液位计 玻璃管液位计超声波液位计
分体式超声波物位计(标 分体式超声波液位计(精 分体式超声波物位计 一体式超声波液位计(雷达液位计
石英管液位计
石英管式双色水位表 X49H平板锅炉水位计 B49H型锅炉双色水位表 彩色石英管液位计浮球液位计
液位变送器
静压高温投入式液位变送 静压投入式液位变送器 直杆式液位变送器 平衡罩式液位变送器 电感式液位变送器 防腐投入式液位变送器 双法兰液位变送器 LY-600系列电容液位计射频导纳物位计
浮球液位开关控制器
浅析潜油电泵专用磁翻柱液位计自动化改造实践
作时间:2019-09-24 16:59:49 来源: 作者:
摘要:某油田采用专用磁翻柱液位计人工调整频率来控制潜油电泵,针对电流间断性尖峰波动时,磁翻柱液位计无法及时采取动作造成过载保护停机的问题,在现有磁翻柱液位计中增加自动调频芯片,通过在自动调频芯片中设定1个合理电流值,当电流波动值超过设定电流值时,磁翻柱液位计自动下调频率,降低电机输出功率,直至运行电流在设定电流值以下;当电流运行平稳后,磁翻柱液位计自动恢复原频率,实现降频、降电流、避免停机风险。现场11口井应用证明:月均减少停机18井次,避免检电泵3井次,增加了产量,减少了稀油浪费,取得了很好的效果。
某油田为奥陶系缝洞型碳酸盐岩油藏,由于油质稠,采用套管掺入稀油方式降黏生产[1-7],为有效举升地层液量,选用举升能力强、排量大的潜油电泵开采[8]。为了满足油井供液变化,地面配套潜油电泵专用磁翻柱液位计用于控制生产。在油井稳定生产阶段,人工调整磁翻柱液位计频率即可实现电泵生产所需排量。随着油井生产复杂化,现有磁翻柱液位计控制方式难以满足生产需求,主要表现为油井出砂、含水波动、稀油和稠油混配不均,造成电流间断性尖峰波动,经常出现过载保护停机[9]。统计发现129口生产井中29口井均不同程度出现电流波动,频繁异常停机,降低了电器绝缘性能,造成稀油和稠油浪费,增大电泵管理难度;频繁启停电泵导致保护器频繁呼吸,保护器提前失效,增大了检电泵风险[10]。因此,急需改进现有磁翻柱液位计控制方式,降低电流波动造成的油井管理难度。
1 解决方案
电泵电流波动通常是油井中稀油和稠油混配不均造成电流突然异常升高而导致保护停机,因此如何及时降低电流峰值,避免电泵停机成为改造的首要因素。通过方案对比及经济评价,小幅改造现有磁翻柱液位计可实现自动控制电流的目标,即通过应用自动调频芯片,达到自动降频、降电流的目的,减少了电泵停机甚至检电泵风险。在现有磁翻柱液位计中安装自动调频芯片,设定1个合理电流值,当油井因出砂、含水、掺稀不稳造成电流波动值超过设定电流值时,磁翻柱液位计自动下调频率,降低电机输出功率,直至运行电流在设定电流值以下;当电流运行平稳后,磁翻柱液位计自动恢复原频率,实现降频、降电流,避免了停机风险。自动调频芯片工作原理如图1所示。

以TH122X1井为例,该井油质稠,黏温拐点深,稀油稠油混配效果差,电流在25~50A时频繁波动,造成电泵频繁停机。为降低管理难度,在该井实施自动调频芯片试验,设定合理电流值为40A,当运行电流超过40A则频率自动下调2Hz,降低了电机输出功率,减少了电泵负载,确保电流在25~40A波动,改造后异常停机次数明显减少,有效提升了生产时效。该井应用自动调频芯片前后电流对比曲线如图2所示。
2 应用效果
自动调频芯片主要用于电流间断性尖峰波动使停机频次高的超稠油区块井,表现为含水波动、稀油稠油混配不均造成电泵电流波动大,已在
11口井现场安装自动调频芯片,主要取得效果见表1所列。
1)通过自动降频方式,有效降低异常电流峰值,月均减少停机18井次,避免检电泵3井次。
2)自动调频芯片确保电泵稳定生产,有效提高生产时效,增加产量1 140t,减少稀油浪费3 500t。
3)自动调频芯片投入少、产出大,11口井投入费用约2.2万元人民币,产出效益401万元人民币。
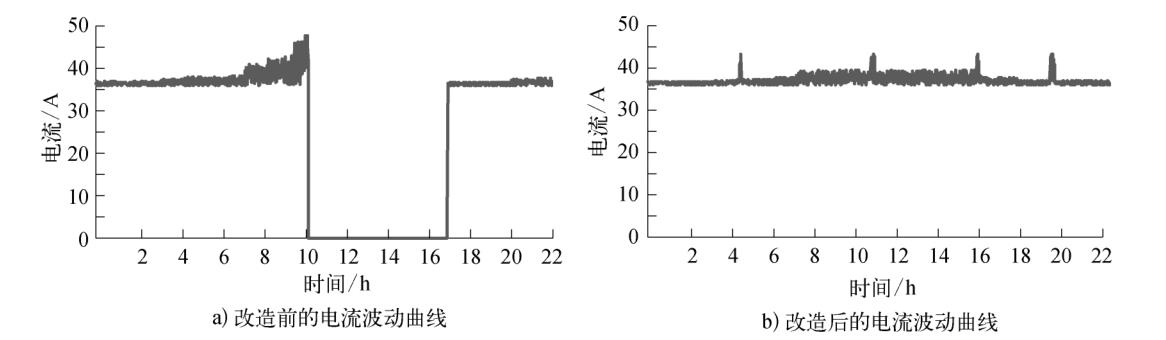
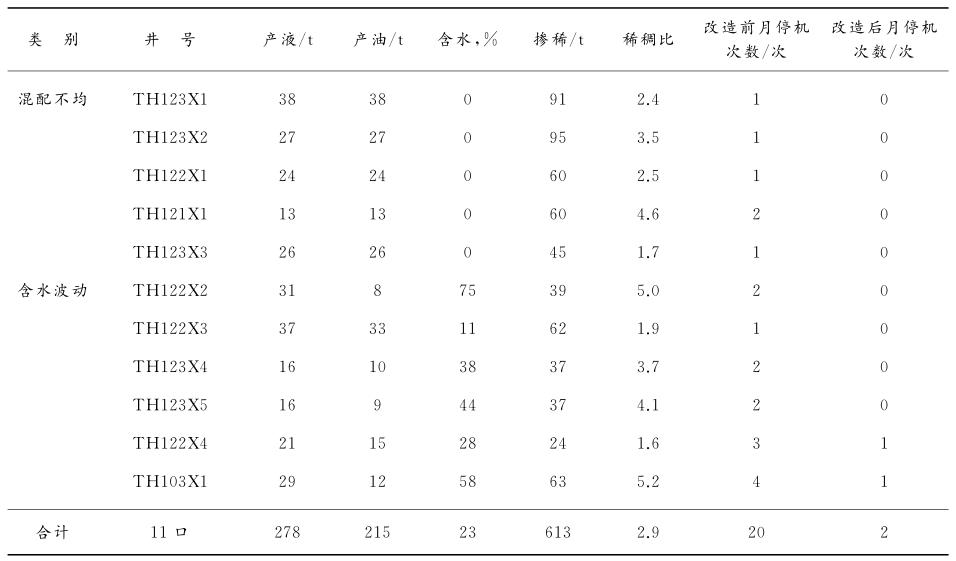
3 结束语
1)自动调频芯片解决了现有磁翻柱液位计无法自动调频的缺陷,满足了复杂油井生产需求,改造成本低,有利于采油厂降本增效。
2)自动调频芯片确保电泵在设定合理电流值下生产,降低现场管理难度,月均减少停机18井次,避免检电泵3井次。
3)自动调频芯片确保电泵稳定生产,有效提高生产时效,增加产量1 140t,减少稀油浪费3 500t
上一篇:如何选择雷达液位计清洗器配件进行快速修复
下一篇:硫酸装置防雷整改的实践与探讨
最新资讯
- [公司新闻] 磁翻板液位计有测量盲区吗 2021-12-06
- [行业新闻] 差压变送器该怎么维护 2021-11-29
- [行业新闻] 浮球液位计保养时注意事项 2021-11-25
- [公司新闻] 磁敏双色液位计与磁翻板液位计有什么区别 2021-11-16
- [公司新闻] 造成磁翻板液位计内浮子下沉的常见原因都 2021-11-10
推荐专题
- [技术专题] 石油储罐液位测量选择雷达液位计后的安装 2012-10-26
- [技术专题] 超声波液位计的优点和清洗方式 2012-10-20
- [技术专题] 怎样选购高温高压型磁翻板液位计 2012-10-20